The Significance of Thorough Welding Inspection in Industrial Applications
In the world of commercial applications, the significance of precise welding examination can not be overstated. As we explore the diverse advantages of attentive welding evaluations, one need to take into consideration the broader implications on security, dependability, and cost-effectiveness in commercial procedures.
Enhancing Architectural Integrity
When it concerns welding assessment in commercial applications, boosting architectural honesty is extremely important. The primary goal of welding evaluation is to guarantee that the welds can birthing the anticipated lots and stress and anxieties they will certainly encounter in service. This involves a comprehensive assessment of the welds' dimensions, alignment, and overall high quality, ensuring they meet the specified standards and codes. Specific examination approaches, such as aesthetic assessment, ultrasonic testing, and radiographic testing, are essential in identifying issues that can endanger the structure's safety and functionality - Welding Inspection Madison.
The importance of keeping architectural integrity in bonded frameworks can not be overstated. Badly performed welds can lead to devastating failings, causing expensive repair work, downtime, and also endangerment of human lives. Assessors play a vital duty in the lifecycle of industrial parts, offering guarantee that the welding process provides the wanted strength and toughness.
Furthermore, progressed technologies, such as phased variety ultrasonic screening and digital radiography, offer boosted capabilities in finding possible weaknesses, enabling rehabilitative measures before concerns rise. By prioritizing the stability of welds via meticulous evaluation, sectors can make certain operational effectiveness and prolong the long life of their infrastructure.
Identifying Welding Problems
Recognizing welding issues is an essential element of making certain the safety and dependability of welded structures. These flaws can endanger the honesty of the whole setting up and, if left unaddressed, might lead to devastating failures. Common welding problems include porosity, fractures, incomplete combination, and undercutting. Each of these problems occurs from certain causes, such as incorrect welding methods, contamination, or insufficient warm control.
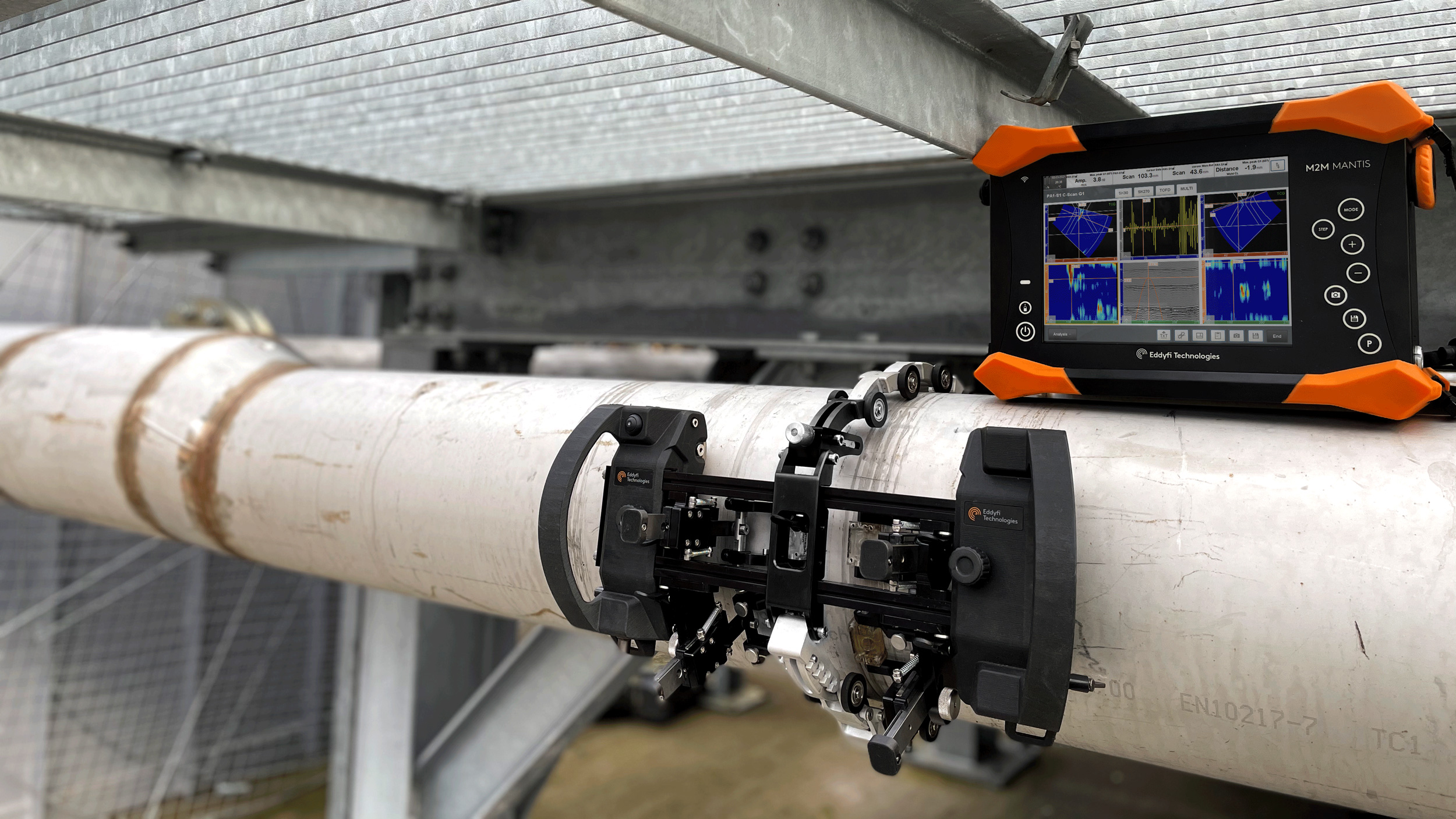
Experienced assessors utilize both visual assessment and progressed non-destructive testing (NDT) techniques, such as ultrasonic or radiographic testing, to identify these defects. The timely recognition and correction of welding defects are critical to maintain the architectural integrity and durability of industrial parts.
Ensuring Conformity Requirements
Preserving the stability of welded frameworks expands past determining issues; it requires adherence to rigorous compliance requirements. Compliance with well established criteria, such as those given by the American Welding Culture (AWS) and the International Company for Standardization (ISO), ensures that welds meet minimal safety and quality demands. These requirements incorporate a large range of criteria, consisting of product requirements, welding treatments, and credentials of welders. Adherence to these requirements is you could try these out vital to protect against architectural failings, which might result in devastating effects in commercial applications.
Regular audits and examinations are necessary in verifying conformity. Inspectors have to possess a thorough understanding of the appropriate standards and be skilled at using different non-destructive screening (NDT) techniques to review weld quality. By making certain that welding practices line up with compliance requirements, firms reduce the threat of non-conformity, which can lead to lawful liabilities and security threats.
Furthermore, keeping conformity not only safeguards architectural honesty but likewise boosts a company's credibility in the sector. Stakeholders and clients are most likely to trust firms that constantly Website show a dedication to quality and safety with strenuous conformity. Hence, ensuring compliance requirements is a critical component in the successful application of welding in commercial applications.
Minimizing Upkeep Prices

The application of sophisticated non-destructive testing (NDT) approaches, including ultrasonic, radiographic, and magnetic fragment assessments, enhances the capacity to discover subsurface flaws without jeopardizing the structural honesty of components. check my site By using these methods, sectors can substantially extend the solution life of their equipment, minimizing downtime and the associated monetary burden of maintenance tasks.
Additionally, a durable welding inspection routine supports the optimization of maintenance timetables, shifting from responsive to anticipating maintenance methods. This aggressive method not just curtails unforeseen failings but likewise simplifies resource allotment, making certain that maintenance efforts are concentrated and reliable. Ultimately, the investment in extensive welding examination is offset by the considerable cost savings understood through decreased maintenance needs, adding favorably to the total operational efficiency of industrial business.
Improving Safety And Security Actions
Although safety is a critical worry in commercial procedures, achieving optimal safety standards needs a specialized focus on the high quality and integrity of bonded frameworks. Welding examination plays a critical role in this context, as it ensures that all connections and joints meet stringent safety criteria. Comprehensive inspections help identify issues such as fractures, porosity, or incomplete blend that can endanger architectural stability. Such flaws, if left unaddressed, present considerable risks, potentially leading to tragic failings.
Methods like ultrasonic screening, radiographic screening, and magnetic particle evaluation permit for detailed evaluation without harming the framework. Implementing a robust high quality control system that consists of normal training for inspectors and welders makes sure adherence to developed safety and security standards.
Finally, promoting a society of safety and security within the company emphasizes the significance of complete welding examinations. Encouraging open communication and collaboration among engineers, welders, and examiners contributes to a shared commitment to security excellence. Welding Inspection Madison. In doing so, sectors can safeguard their procedures, protect employees, and keep public trust fund

Conclusion
Extensive welding inspection is crucial in industrial applications, dramatically improving architectural integrity and integrity. Ultimately, the thorough implementation of welding evaluations plays a crucial function in keeping operational effectiveness and safety and security in industrial settings.
As we discover the multifaceted benefits of attentive welding inspections, one need to take into consideration the broader ramifications on safety and security, reliability, and cost-effectiveness in industrial procedures.
The primary goal of welding assessment is to make certain that the welds are capable of bearing the expected tons and stress and anxieties they will certainly run into in solution. Effective welding evaluation plays an important duty in decreasing these costs by guaranteeing the stability and durability of welds, consequently minimizing the threat of early failings.Thorough welding evaluation is vital in commercial applications, dramatically boosting architectural honesty and integrity. Inevitably, the attentive implementation of welding examinations plays a crucial duty in keeping functional performance and security in commercial settings.